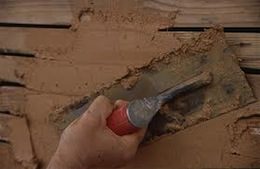
Natural building is similar to green building. It seeks to reduce the environmental impact of our dwellings without sacrificing health or comfort. Green building often includes materials that many see as unhealthy or not natural. It’s tricky defining natural building systems and we urge people to view the big picture of this subject with open minds.
Size Matters
We make some generalizations in this post, and the size of the home, building or dwelling is the detail that largely governs this subject’s appropriateness. Homes with tiny square footages (<400 square feet) make it hard to measure costs, impacts and outcomes making them tough to generalize about. Small homes (400-1200 sqft) also defy typical expectations but their material and energy usage becomes more important on the higher end of the range. Tiny homes use such small amounts of materials, labor and energy that their environmental impacts get tough to measure compared to average size homes. Tiny homes make more sense to try unconventional construction methods.
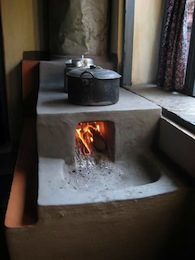
Indoor combustion is more unhealthy than materials
Most natural building seems to rely on indoor combustion to keep comfortable during the heating season.
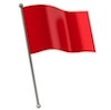
This is a huge, dirty red flag. Wood stoves, Rocket Mass Heaters RMH, or combustion inside the living space almost always pollute the indoor-air more than suspect building materials. Reducing indoor air pollution is a holistic subject, but building researchers typically find higher amounts of measured pollutants from indoor combustion than they do from unhealthy building materials.
Wood stoves and Rocket Mass Heaters RMH are major pollution sources to be aware of. They generate serious pollutants which are easily measured. Smoke, soot, ash, dust and particles from wood or other biomass are dirty and have measurable health concerns that should be avoided whenever possible.
Many avoid unnatural building materials because of the damage to society and environment. Studies point to wood smoke as a major source of outdoor-air pollution. Some stoves burn cleaner than others but even the cleanest burning appliances do not eliminate risks. Burning wood has negative effects on society and the environment, perhaps equal to or more than suspect building materials.
Walls are only one instrument in a big orchestra of music
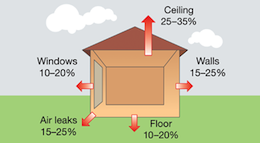
Analysis paralysis is common with building design and wall construction gets the most attention for perceived opportunities yet leads to the most frustration, especially for natural building. It’s common to get carried away specifying unconventional, natural building materials for walls, only to choose more typical construction materials for the rest of the building elements. As specific parts are addressed, others become bigger players. Make up for weak wall performance elsewhere or don’t build thermally weak walls. Staying balanced in building envelope design is desirable to achieve reasonable costs and performance.

What is a Building Envelope? It’s important to understand the role of the building envelope and its impact on energy use, comfort and durability. Wall area is easy compared to the big picture. Whether building with earth, wood or stone, identifying and implementing a continuous building envelope is priority #1.

The Blower Door Test is used to prove the airtightness (or draftiness) of a home or building. There is nothing unnatural about stopping unwanted air movement. It’s considered the most cost-effective way of increasing comfort and reducing energy use. Not all natural building projects will choose to use a blower door to verify airtightness but be aware of the physics regarding this primary concern for building envelopes; comfort, energy use, and durability. Uncontrolled air movement is the 2nd biggest moisture concern after bulk water leaks.

Outdoor-Air Ventilation is the best way of addressing indoor air quality. No matter how natural building materials are, indoor-air needs to be exchanged with outdoor-air. Passive ventilation is natural but offers little control when indoor-air needs conditioning. Mechanical ventilation seems to be considered unnatural by some, but the simple technology of a fan is hardly a major concern. It’s the main way researchers have been able to improve indoor-air pollution measurements.

Breathing Walls always pops up in discussions of natural building. Confusion and misinformation is rampant with this topic. If you think walls need to breathe, make sure you know what that means. Stopping air-movement is a different concern and measurement than vapor permeability. Walls and other building envelope components are evaluated with three main performance criteria: airtightness, insulation (R-value) and vapor permeability. Control airflow, control heat and allow materials to dry.
Thermal Mass TM can be good, but not for exterior walls.
This is a relevant topic for improving natural building performance but it’s importance is way overblown. In general, thermal mass should be completely inside the thermal envelope. There are few climates where it makes sense to use thermal mass as the exterior walls of a home or building. Oak Ridge National Labs has done the most research on thermal mass performance. Their research suggests that only high desert climates with wide diurnal temperature swings benefit from thermal mass exterior walls. Homes that put the TM completely inside the thermal envelope do better but the energy advantages are so small, they get hard to measure.
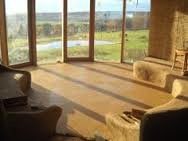
Thermal mass is heavy which tends to make it expensive and environmentally wasteful. Most natural building techniques that implement thermal mass in exterior walls are labor and time intensive. For small to tiny owner-built projects, exterior walls of thermal mass can make more sense but for most small to average size homes, they waste too much heat in our climate’s winter. Most homes contain plenty already and slabs on grade make the most sense for additional TM.
A Green Builder Advisor article all about thermal mass. More on thermal mass in these posts:
Radiant Floor Heating
Passive Solar Design
Building code challenges
Some people are so enamored with a particular natural building technology, that they will move or choose a location with no building code enforcement. It’s tougher getting code authorities on board with unconventional construction details. Most code authorities are reasonable and allow exceptions for innovative design. It requires a certain amount of professionalism, communication and sometimes the help of a structural engineer. Even those building outside of government oversight can include these energy and ventilation codes as a minimum for a cost-effective level of performance, comfort and health.
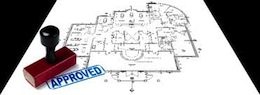
The easiest path for code approval involves using common construction methods. This doesn’t have to mean unnatural. Common construction details always have natural alternatives. If there is a particular detail that gives a code department pause, step back and evaluate how important it is for the big picture. There is usually a readily approved strategy that can meet a project’s needs for similar costs and performance.
Natural Building Materials for Exterior Walls
Walls only account for 10-25% of a home or dwelling’s building envelope performance so remember that these natural options are only part of the picture. The weaker the walls, the more they influence energy performance of the entire structure. This is a summary on the most common natural building materials for Asheville, Western North Carolina and most East coast US climates.
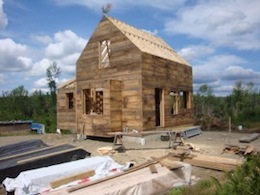
Stick (Wood) Framed Walls
Our country’s most common way of framing walls is as natural as it gets. 2x studs can be from local or sustainably managed forests and do not rely on older growth trees that log and timber framing tends to use. Insulation, structural sheathing and weather barriers are what most of those building naturally seem to have problems with. Timber, board sheathing and let-in bracing can eliminate the need for engineered wood products but it’s critical to make these structures air-tight (draftproof). Air-tight can still be vapor permeable. Proper flashing and rainscreens for exterior finishes are most important for durability.
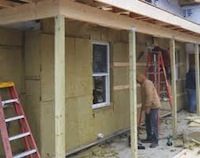
Most of our nation’s oldest homes are built this way and are notorious energy wasters, mainly due to their lack of airtightness and insulation. One of the reasons they last so long is the enormous amounts of energy needed to keep them comfortable helps dry them out. As we add insulation and increase airtightness to make the insulation effective, we need to be extra mindful about keeping bulk water out and making sure that vapor profiles allow the assembly to dry in at least one direction. Weatherproof window installation is often overlooked by conventional and natural builders.
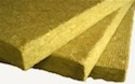
Mineral wool is a quality insulation accepted by both conventional and natural builders. It’s used to insulate framing cavities but for best performance, use it in board form to wrap exterior walls. This is a more continuous insulation helping control energy loss through the framing and structural members; reducing thermal bridging.
Log and Timber Walls
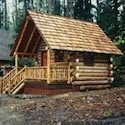
This can be an appropriate choice for small to tiny homes. It’s an old and proven form of construction using familiar materials and methods and it’s readily accepted by building codes. Solid wood is a good insulator compared to earth or stone but it’s a poor performer compared to most forms of insulation. With an average R-value of 1 per inch, solid wood falls well short of prescriptive code minimum insulation performance in common overall thicknesses (6-12″). Some see the material as rustic, others see it as a black hole of energy use.

More concerning than its R-value is it’s airtightness problems. With its constant expansion and contraction, solid wood is difficult to keep airtight if you ever manage to get it airtight in the first place. For the exterior finish, it’s an infamous material to maintain but smart design can help. Deep overhangs better protects vulnerable exposed wood and this material needs regular maintenance. Log homes are known for dark interiors due to deeper overhangs and darker interior wall colors. For more; US DOE log home resource, Pros and Cons of log homes and a good video on traditional Finnish log home building.
Timber Framing (Post and Beam)
An ancient form of construction appropriate in areas with good wood resources. It’s similar to stick framing, but the larger pieces of wood are more resistant to getting wet. Bigger pieces of wood usually means higher material and labor costs. Other forms of wall construction often rely on timber for the structural needs and infill between or outside the wood.
Strawbale Walls
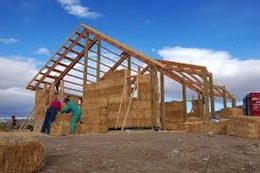
This natural material’s best attribute is its insulation value. At R25-45, strawbale walls exceed prescriptive insulation minimums and achieve net-zero optimized or passive house certification levels of thermal performance (with blower door proven airtightness). This material can be done appropriately in our climate but takes exceptional design and construction details to alleviate the indoor-air quality concerns. When straw gets wet or moist, it’s an excellent food for fungi, mold and mildew which is obviously not healthy for indoor-air.
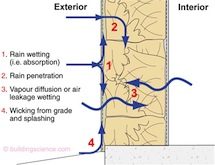
Climate matters with strawbale and our climate is considered risky. Many strawbale experts question its role in humid climates like ours. Its track record appears sketchy but many examples of failure can be applied to improper material handling, design and installation details. Our climate’s year round humidity is higher than strawbale’s safe range which makes the material so challenging. This strawbale article by building scientist John Straube is required reading for those building with strawbale.
Strawbale.com is a good resource and for those with all-natural mindsets, even the experts dont recommend natural twine. A catastrophic strawbale anecdote, a strawbale overview for inspectors, and more pros and cons of strawbale.
Stone
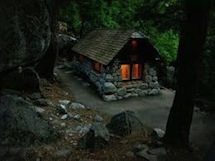
Stone is an ancient building material with many desirable aspects, most appropriate in areas with rich stone resources and common as a foundation material. Unless the structure is very small, it’s thermal weakness precludes it from exterior walls unless it is used as a veneer. Stone’s R-value is ~.25 per inch and is better used as a thermal mass. If used as part of the building envelope with no additional insulation or thermal break, its resistance to heat flow is a huge problem during our winter heating season. The best use of stone in our climate for exterior finishes is as a veneer, hardscape, or plinths for posts.
Earth
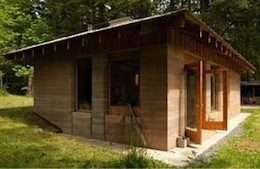
Earthen walls come in many forms and I tend to lump them into the same category. Adobe, cob, blocks, rammed earth, and earthbags all deserve their own blog posts but they also share the same problem in our climate; they are poor at resisting heat flow. They all have crummy insulation values (R .25- R1 per inch) which makes them a poor performing exterior wall material in our climate’s cold season.
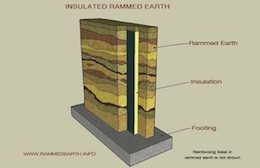
There are ways of addressing the lack of insulation aside from building so small that energy problems are reduced. I came across the image on the right, of an insulated rammed wall that would do a better job at resisting heat flow. Earthen walls are known for their high labor costs but for those supplying their own labor, small projects and sites of good dirt, it makes for a compelling form of natural building.
Earth Sheltered, Bermed, Underground Walls
Moving a home’s walls below grade reduces insulation needs but increases chances of radon, water and moisture damage. Ground temperatures are less extreme than air temperatures so we typically dont need as much R-value to control heat flow. This also forces designers to eliminate windows, which tend to lose heat in winter and gain unwanted heat through direct solar gain during the summer. Choosing windows offers more guidance for some of these concerns.

Challenges are usually increased by building underground. Almost any type wall can be used underground with the exception of strawbale. Passive radon systems are important for controlling soil gases. Water or damp proofing details for walls exposed to the earth are critical. The best systems use free-draining backfill, like clean gravel, protected by geotextile or fabric to keep fine soils from infiltrating the gravel. It should all be drained to daylight, preferably with a simple pipe system that can be snaked or cleaned in the future. There are many natural materials available to deal with these physics.
Passive Annual Heat Storage PAHS is the theory that underground construction can reduce or eliminate space conditioning systems. The theory goes that insulation is placed away from the underground walls and the earth between can be used as additional thermal mass to store enough heat in the summer to make it through the winter. In our climate, humidity is the main problem and underground homes typically see higher moisture loads. PAHS is unproven with nearly zero case studies to follow. Research suggests homes perform much better with insulation right at the wall.
The best opportunity for this type of construction is a walkout basement. A sloping site allows one side of the home to be bermed with the other open to daylight, views and sunshine. Walkout basements are common in our region and perform excellent with the right water and moisture management details. Building Science Corporation is a great resource and we recommend starting with understanding basements. Most pictures and diagrams feature conventional construction materials but natural building materials are easily substituted.
Cordwood
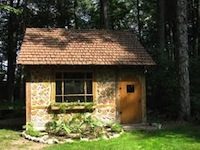
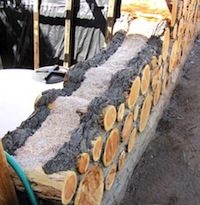
Cordwood is appealing for its DIY nature and readily available materials. Its typically a poor performer for exterior walls. Performance is improved by using an insulative material between the interior and exterior mortars but don’t expect much of an improvement. The substantial thermal bridging of the logs, end-to-end probably result in total wall R-values of ~R1 per inch, needing painfully thick walls for code minimum prescriptions. The bigger concern is these walls are very difficult to make airtight. Many are drawn to the aesthetics and they make good sense for garden sheds and tiny homes. Cordwood.org
Is Concrete Natural?
This contentious material is considered by some to be unnatural. It’s the most used construction material in the world and is responsible for the vast majority of the world’s pollution related to building and construction. It has a high embodied energy to make and because it’s heavy, has high transportation related environmental impacts.
Sand + Gravel + Limestone + Water
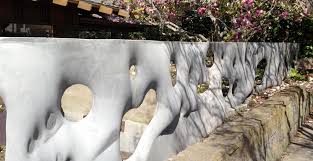
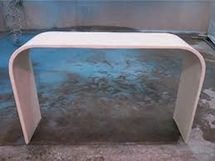
Concrete is an ancient building material and the end product is typically safe and benign, other than the dust created by cutting it. The simple ingredients are abundantly available across the planet. It’s the most used building material for good reason; a pourable, formable rock whose durability outlasts most other building materials when done right. It is extremely versatile and we continue to find new and creative ways to use it in architecture and building.
Portland Limestone Versus Other Limestone
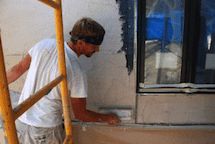
Some concrete detractors point to Ordinary Portland Cement OPC as the main problem with modern concrete. Portland cement, requires roughly 2x more kiln energy than older forms of slaked or hydraulic lime. For stucco or plasters over natural building materials like strawbale, many choose lime plasters instead of portland. Many recipes of portland stucco call for certain parts hydraulic lime.
I find it odd some natural builders consider hydraulic lime natural but portland unnatural. Is it because portland was fired in a kiln at 2600 degrees instead of 1800 degrees? Is it because portland is newer than traditional lime? Some applications like plaster, make sense for hydraulic lime. Other uses like floors, call for portland. Performance, costs and availability usually affect the environment, just as much as a material’s overall volume or scale.
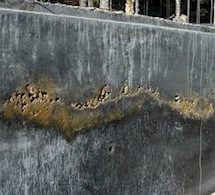
Concrete is mostly sand and gravel
Modern concrete is mostly (2/3) aggregate. Only 1/3 of concrete is limestone and its possible to substitute some of this limestone for coal ash or other pozzolans. Size and volume of concrete needed are as important as the size of the dwelling. Some applications like pre-cast concrete panels use very small amounts of concrete for the function they provide. The concrete plant’s proximity to railroad lines and quarries can reduce the material’s impact as can proximity of the project to the concrete plant. Being abundantly available, safe for indoor-air, affordable, durable and approved by building codes, keeps this material a fine choice for natural building projects that use it in smart ways.
Energy Before Materials
Concrete’s high embodied energy is its main weakness but at least there is a defined end point. Monthly, dirty energy bills are the true metric for the sustainability of a home or building. Don’t let obsessions with finishes and materials lead to wasted dirty energy costs or increased indoor combustion risks.
I hope to add more to this post and want to reiterate that natural building and green building share the same philosophies. Natural buildings should be paying attention to the same priorities as green building. A natural building that pollutes its environment with woodsmoke or other dirty, monthly energy costs is little more environmentally friendly than their conventionally built neighbors.
Green Building’s Top 3 Priorities
Heating and Cooling in WNC
Brian Knight is owner of Springtime Homes, green builders in Asheville, specializing in indoor-air quality.